
Galvanized iron wire, soft annealed, electro galvanized and hot
dipped galvanised, pvc or epoxy coated into colors. Made of high carbon, medium and low carbon steel.
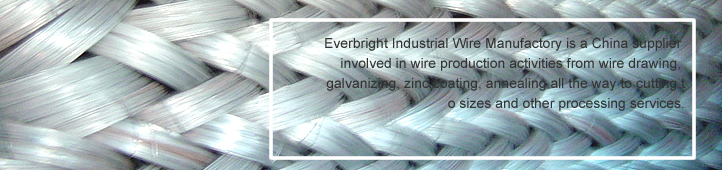
Spring Steel Wire Technological Properties
Everbright supplies Cold Drawn Spring Steel Wire with guaranteed excellent properties meeting EN 10270 European Standard and similar international standards.
Our spring steel wire is manufactured meeting European Standard and supplied with tested properties as following.
Coiling Test
In order to assess the uniformity of the wire in the coiling deformation and its surface condition, the coiling test is carried out on wire with a diameter up to 0,70 mm for the spring wires with medium and high tensile strength for still and dynamic stress requirements.
The coiling test shall be carried out in the following manner:
A test piece - approximately 500 mm in length - shall be closely wound, under slight but reasonably uniform tension on a mandrel three to three and a half times the nominal diameter. The mandrel diameter shall however be at least 1,00 mm. The close coil shall be stretched so that after releasing the stress it sets to approximately three times its original length.
The surface condition of the wire and the regularity of the spring pitch and individual windings shall be inspected with the test piece in this condition.
In the test, the tested steel wire shall exhibit a defect-free surface without splits or fracture, a uniform pitch of the turns after coiling and a fair dimensional regularity of its diameter.
Although the usefulness of the coiling test is not generally recognized, it has been retained since it offers the possibility of revealing internal stresses. If doubtful test results are obtained the wire concerned should not be rejected immediately but efforts should be made by the parties concerned to elucidate the cause.
Torsion Test
For assessing the deformability, fracture behaviour and surface condition the torsion test shall be carried out for all wire grades on wires in the nominal diameter range over 0,70 mm to 10 mm. The minimum number of turns specified in Table 3 for diameters up to 7,00 mm is mandatory. For wires exceeding this size they shall be taken only as indicative values.
For the torsion test:
The tested wire shall be clamped into the device in such manner that its longitudinal axis is aligned to the axis of the clamping heads and the test piece remains straight during the test. One clamping head shall be turned at as uniform a speed of rotation as possible (not exceeding one rotation per second) until the test piece fractures. The number of complete rotations of the turning clamping head is counted. The free length between grips shall be uniformly 100 x d (d = nominal diameter of the wire) with a maximum of 300 mm.
In executing the test, the required number of turns shall be achieved before the test piece fractures. The fracture of the torsion test piece shall be perpendicular to the wire axis.
Spring back resilience cracks or spring back fractures (“spoon” or “secondary” fractures) are not considered in the evaluation. In each case a uniform distortion of both fragments shall be present although the pitch of the turns need not be the same in the two parts. In the case of grade high tensile strength spring wire for dynamic spring stress, no surface cracks visible to the naked eye shall be present after the torsion test.
Wrapping Test
The wrapping test may be applied to cold drawn steel wire with a diameter equal or less than 3,00 mm. The wire shall not show sign of fracture when close wrapped eight turns around a mandrel of a diameter equal to that of the wire.
The wrapping test shall be carried out according to EN 10218-1:
The wire shall be wrapped 8 turns around a mandrel with a diameter equal to the wire diameter.
Bend Test
Where requested the bend test may be applied to wire with a diameter greater than 3,00 mm. The wire shall withstand the test without any sign of failure.
For the bending test, a wire sample of sufficient length shall be bent in U form around a mandrel with a diameter equal to twice the wire diameter for sizes above 3,00 mm to 6,50 mm and equal to three times the wire diameter for sizes above 6,50 mm. For practical reasons the wire shall be deemed to have met the requirements of this standard if it withstands bending around a mandrel smaller than the one specified. In carrying out the test the wire shall be free to move longitudinally in the forming device.
In some applications the material is severely deformed by bending. Such is the case for extension springs with tight hooks, springs with bend on legs, spring wire forms, etc. In such cases the bend test provides for a wire test very close to the actual use.

- Galvanized Iron Wire
- ASTM A 641 Galvanized Wire Standard
- Cold Heading Wire
- Brass Coated Wire
- Hot Dip Galvanized Wire ASTM A-475
- Trellis Wire
- High Carbon Galvanized Steel Wire
- Nose Wire
- Phosphate Coated Steel Wire
- Spiral Binding Wire
- Champagne Cork Wire
- PC Strand
- Chain Link Security Fence
- Galvanized Welded Wire Mesh
- Galvanized Hexagonal Wire Mesh
- Galvanized Wire Mesh Fence
- Galvanized Core Wire for ACSR
- Galvanized Steel Stranded Core Wire
- Galvanized Wire (GI Wire)
- Oil Tempered Steel Wire
- Electro Galvanized Iron Wire
- Hot Dipped Zinc Plated Wire
- Spring Steel Wire
- High Carbon Spring Steel Wire
- Technical Details of Hot Dip Galvanized Wire
- Galvanized Steel Wire
- Copper Coated Steel Wire
- Hot Galvanized Wire Products for Portugal Market
- Oval Wire
- Fencing Wire
- Mild Steel Wire
- Low Carbon Steel Wire
- Redrawing Wire
- Annealed Wire
- Black Iron Wire
- Binding Wire
- Wire Ties
- Loop Tie Wire
- Rebar Tie Wire
- Cut Wire
- Stitching Wire
- Armoured Cable Wire
- Welding Wire
- PVC Coated Wire
- PVC Coated Steel Wire Technical Parameter
- Coil Wire
- Spool Wire
- Barbed Wire
- Baling Wire
- Staple Wire
- Hose Wire
- Music Wire
- Brush Wire (Wire for Brushes)
- High Tensile Wire
- Razor Wire
- Galvanized Wire for Armouring Cable
- Galfan Wire
- Galvanized Wire Mesh
- Galvanized Flat Stitching Wire
- Lashing Wire
- Galvanized Wire Rope